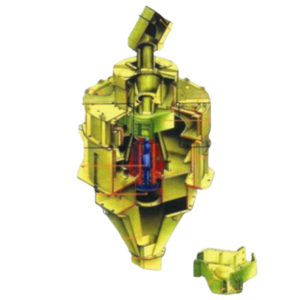
Vertical Shaft Impactor
Crush the hardest and biggest stones
What is a VSI Crusher?
A Horizontal Shaft Impact (HSI) crusher are essential in the world of stone crushing for producing high-quality aggregate, cubical-shaped products in the construction and mining industries. The process involves a high-speed rotor with wear-resistant tips that accelerates the material through centrifugal force. As rocks collide against each other, they break into smaller particles, creating a more cubical product compared to traditional crushers. This unique crushing action makes VSI Crushers highly effective in various applications, from construction to mining.
Specifications include:
- 2-stage and 3-stage
- Capacity : 20 TPH to 500 TPH
- Feed size : 300 – 700 mm and below
- Output size : 40 mm and below
- Price : INR 1.0 – 5.5 crore
- Power Source : Electricity or diesel generators
- Flexibility : Customized based on specific requirements
VSI Crushers Assembly Process
-
Frame Assembly: The foundation of a VSI crusher is its robust frame. Skilled technicians meticulously assemble the frame, ensuring precision and durability. The frame serves as the backbone, supporting the critical components that follow.
-
Rotor Construction: The heart of every VSI crusher is its rotor. Crafted from high-quality materials and precisely balanced, the rotor undergoes rigorous assembly. Technicians attach the wear-resistant tips, ensuring optimal impact velocity and extended operational life.
-
Chamber Configuration: The crushing chamber is carefully configured to maximize efficiency and product quality. Skilled workers assemble the chamber components, creating the perfect environment for the high-speed rotor to deliver effective crushing.
-
Drive System Integration: The powerful drive system is integrated with precision, connecting the motor to the rotor. This step ensures the seamless transfer of power, allowing the crusher to operate at the required speed for optimal performance.
-
Finishing Touches and Quality Checks: Before a VSI crusher leaves the assembly line, it undergoes meticulous quality checks. Every detail is inspected, from the alignment of components to the functionality of safety features. Technicians add the finishing touches, ensuring each crusher meets the highest industry standards.
Types of VSI Crushers:
Open Rotor and Closed Rotor VSI Crushers:
- Open Rotor: Allows larger feed sizes and is suitable for crushing softer materials.
- Closed Rotor: Ideal for tougher, more abrasive materials and offers better control over the product shape.
Rock-on-Rock and Rock-on-Steel VSI Crushers:
- Rock-on-Rock: Crushing occurs between the rocks themselves, delivering superior shaping of the final product.
- Rock-on-Steel: Utilizes a crushing chamber lined with steel components, suitable for high-abrasion applications.
Static and Dynamic VSI Crushers:
- Static: Designed for stationary installations, providing a cost-effective solution for specific production needs.
- Dynamic: Mounted on mobile platforms, offering flexibility and adaptability for on-the-go crushing requirements.
Checklist for Choosing the Best VSI Crusher:
- Material Characteristics: Consider the hardness, abrasiveness, and size of the feed material.
- Rotor Type: Choose between open and closed rotors based on material requirements.
- Crushing Chamber Configuration: Opt for rock-on-rock or rock-on-steel configurations based on desired final product characteristics.
- Capacity and Throughput: Ensure the crusher can handle the required production capacity and throughput for your application.
- Maintenance Accessibility: Select a VSI Crusher with easy access to key components for simplified maintenance.
- Wear Parts Longevity: Evaluate the wear-resistant components’ durability to minimize downtime and maintenance costs.
- Power Efficiency: Consider the energy efficiency of the VSI Crusher for cost-effective operation.
- Installation Flexibility: Determine whether a static or dynamic VSI Crusher suits your operational needs.
Why Choose HPPA Vertical Shaft Impact Crushers?
Durability and Wear Resistance:
- Problem: VSI crushers often face issues related to wear and tear, affecting the overall lifespan of the equipment.
- HPPA Solution: HPPA Crushers are designed with high-performance materials and advanced engineering, providing superior durability and wear resistance. This ensures a longer lifespan and reduced maintenance costs.
Versatility and Adaptability:
- Problem: Some VSI crushers may struggle to adapt to different types of feed materials and operating conditions.
- HPPA Solution: HPPA Crushers are known for their versatility, capable of handling a wide range of materials and operating conditions. This adaptability ensures efficient performance across diverse applications.
Energy Efficiency:
- Problem: Inefficient VSI crushers may consume excessive energy, leading to higher operational costs.
- HPPA Solution: HPPA Crushers are designed with a focus on energy efficiency, utilizing advanced technologies to optimize power consumption. This results in cost savings and environmentally friendly operation.
Ease of Maintenance and Serviceability:
- Problem: Complex maintenance procedures and difficulties in accessing key components can lead to downtime and increased operational challenges.
- HPPA Solution: HPPA Crushers are engineered for easy maintenance and serviceability. They feature user-friendly designs that facilitate quick access to key components, minimizing downtime and streamlining maintenance tasks.
Particle Shape Control:
- Problem: Inconsistent particle shape produced by VSI crushers can impact the quality of the final product, especially in industries requiring precise specifications.
- HPPA Solution: HPPA Crushers offer advanced control over particle shape, ensuring a consistent and high-quality output. This is crucial for industries such as construction and mining, where specific particle shapes are often required.