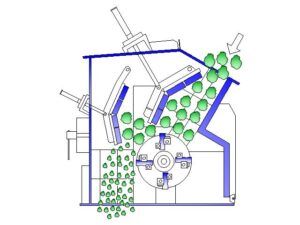
Horizontal Shaft Impact Crusher
Crushing solutions that matter
What is a HSI Crusher?
A Horizontal Shaft Impact (HSI) crusher is a type of crusher that utilizes a horizontal shaft to impel the material against the breaker plates. The HSI crusher consists of a rotor that rotates horizontally, a series of breaker plates that impact the material, and a chamber where the material is fed. The material is crushed or shattered by the repeated impacts, and the resulting product exits the crusher through openings at the bottom.
Specifications include:
- 2-stage and 3-stage
- Capacity : 20 TPH to 500 TPH
- Feed size : 300 – 700 mm and below
- Output size : 40 mm and below
- Price : INR 1.0 – 5.5 crore
- Power Source : Electricity or diesel generators
- Flexibility : Customized based on specific requirements
HSI Crushers Assembly Process
- Frame Assembly: The assembly process typically starts with the construction of the crusher frame. This includes welding or bolting together the main frame components to create a rigid structure that can support the other parts of the crusher.
- Rotor Assembly: The rotor is a key component of the HSI crusher. It consists of a central shaft with several horizontal discs (rotor discs) mounted on it. The discs usually have attached blow bars or hammers that impact the material. During assembly, the rotor discs are mounted onto the rotor shaft, and the blow bars or hammers are attached to the discs. The proper alignment and balance of the rotor are crucial for the crusher’s efficient operation.
- Breaker Plates Assembly: The breaker plates, also known as impact aprons, are installed in the crushing chamber. These plates serve to redirect and control the material flow within the crusher. The breaker plates are often adjustable to control the size of the crushed product. Proper alignment and spacing of the breaker plates are important for achieving the desired product size.
- Feeding System Assembly: The feeding system includes components such as a feed hopper and a feeder. The feed material is typically loaded into the hopper, and the feeder regulates the material flow into the crusher.
- Drive System Assembly: The drive system consists of components like motors and belts that power the rotation of the rotor. This assembly ensures that the crusher can operate at the desired speed and capacity.
- Safety Features Installation: Safety features such as guards and emergency stop systems are installed to ensure the safe operation of the HSI crusher.
- Testing and Quality Assurance: After assembly, the crusher undergoes testing to ensure that all components are functioning correctly and that safety standards are met.
Types of HSI Crushers:
- Primary HSI Crushers: Used for initial size reduction of large materials.
- Secondary HSI Crushers: Further refine the crushed material after it has been processed by a primary crusher.
- Tertiary HSI Crushers: Used for the third stage of crushing, producing finer particles.
- Stationary and Portable HSI Crushers: Available in both stationary and portable configurations to suit different application needs.
Checklist for Choosing the Best HSI Crusher:
- Application Requirements: Determine the type of material you need to crush and the required end product specifications.
- Capacity and Throughput: Ensure that the crusher can handle the required capacity and throughput for your specific application.
- Adjustability: Check if the crusher has adjustable curtains or settings to control the size of the final product.
- Wear Parts: Evaluate the ease of access and replacement for wear parts such as hammers, blow bars, and liners.
- Maintenance Requirements: Consider the maintenance requirements and downtime associated with the crusher.
- Feed Size: Ensure that the crusher can handle the maximum feed size of your material.
- Energy Efficiency: Consider the energy efficiency of the crusher to optimize operational costs.
- Safety Features: Check for safety features and protocols to ensure a secure working environment.
- Cost: Consider the initial cost as well as operating and maintenance costs to determine the overall cost-effectiveness.
- Brand Reputation and Support: Choose a reputable manufacturer with good customer support for technical assistance and spare parts availability
Why Choose HPPA Horizontal Shaft Impact Crushers?
- Performance and Efficiency:
- Problem: Evaluate the overall performance and efficiency of the HSI crusher, including factors such as throughput, reduction ratio, and energy consumption. Look for a brand that consistently delivers high performance in various applications.
- Solution: HPPA Crushers may offer enhanced performance through advanced parallel processing architecture, optimizing the crushing process for higher efficiency and better overall results.
- Wear Parts and Maintenance:
- Problem: Analyze the wear parts and maintenance requirements of the HSI crusher. Choose a brand that offers durable wear parts and provides easy access for maintenance, reducing downtime and operational costs.
- Solution: HPPA Crushers may incorporate innovative design features that minimize wear and tear on critical components, leading to longer lifespan and reduced maintenance needs.
- Versatility and Adaptability:
- Problem: Consider the versatility of the HSI crusher in handling different types of materials and applications. Opt for a brand that offers adaptable configurations to suit various crushing needs.
- Solution: HPPA Crushers may provide enhanced adaptability through advanced control systems and automation, allowing for precise adjustments to accommodate different feed materials and operational conditions.
- Safety and Environmental Impact:
- Problem: Prioritize safety features and environmental considerations. Ensure that the chosen brand adheres to safety standards and minimizes environmental impact through dust suppression systems and other measures.
- Solution: HPPA Crushers may incorporate advanced technologies that enhance safety, such as intelligent automation for real-time monitoring and control, contributing to a safer working environment.
- Customer Support and Training:
- Problem: Evaluate the level of customer support and training provided by the brand. A reliable supplier should offer comprehensive training programs and responsive support to address any issues promptly.
- Solution: HPPA Crusher manufacturers may provide extensive training and support services, leveraging advanced technologies for remote diagnostics and troubleshooting to ensure efficient ongoing operation and minimal downtime.