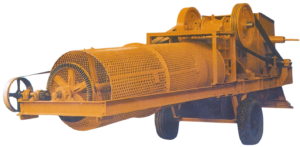
Rotary Screen
Seamless Rotary Screening Experience
What is a Rotary Screen?
A Rotary Screen, also known as a trommel screen, is a mechanical screening machine used to separate materials by size. Its design involves a cylindrical drum that rotates, allowing efficient screening of various materials such as crushed stones, minerals, and aggregates.
Specifications include:
- 2-stage and 3-stage
- Capacity : 20 TPH to 500 TPH
- Feed size : 300 – 700 mm and below
- Output size : 40 mm and below
- Price : INR 1.0 – 5.5 crore
- Power Source : Electricity or diesel generators
- Flexibility : Customized based on specific requirements
Advantages of Rotary Screen
- Versatility and Customization: Easily adaptable for various materials, allowing customization for different project needs.
- Effective De-Watering: Excels at de-watering during screening, crucial for controlling moisture levels in stone crushing operations.
- Compact Footprint: Space-efficient design allows installation in areas with limited space without sacrificing screening capacity.
Rotary Screen Assembly Process
-
Frame Construction: The foundation of the rotary screen is its robust frame. High-quality materials, such as steel, are used to construct a sturdy framework that provides support for the entire structure. Welding or bolting techniques are employed to assemble the frame components securely.
-
Drum Installation: The cylindrical drum, a critical component of the rotary screen, is carefully installed onto the frame. Precision is key to achieving the desired angle of inclination, as it directly impacts the efficiency of material movement and separation.
-
Perforated Screen Integration: Next, the perforated screen, featuring strategically placed openings, is fitted onto the drum. The type and size of the openings can be customized based on the specific requirements of the material being processed. This customization ensures that the rotary screen can effectively handle a diverse range of materials.
-
Motor and Drive System: An efficient motor and drive system are then integrated to power the rotary motion of the drum. Proper alignment and calibration are crucial at this stage to ensure smooth and reliable operation.
-
Support Structure and Guards: Additional support structures and safety guards are added to enhance the overall stability and safety of the rotary screen. These elements not only protect operators but also contribute to the longevity of the equipment.
-
Testing and Quality Control: Before the rotary screen is ready for use, thorough testing and quality control checks are conducted. This ensures that the assembled equipment meets the highest standards of performance and durability.
Types of Rotary Screen:
- Trommel Screens: Standard Trommel: Ideal for general screening purposes. Inclined Trommel: Offers enhanced screening efficiency due to its tilted design.
- Vibrating Trommel Screens: Combines vibration and rotation for improved material separation.
- Drum Scrubber Screens: Designed for washing and scrubbing of materials, ensuring optimal cleanliness.
- Disc Screens: Uses rotating discs instead of a cylindrical drum for specialized screening.
Checklist for Choosing the Best Rotary Screen:
- Material Characteristics: Understand the properties of the material being processed, including size, density, and moisture content.
- Screening Efficiency: Evaluate the screen’s efficiency in terms of throughput and particle separation to meet production requirements.
- Screening Capacity: Determine the required screening capacity based on the volume of material to be processed.
- Mesh Size and Configuration: Select the appropriate mesh size and configuration to achieve the desired particle size distribution.
- Durability and Maintenance: Choose a screen with durable construction and easy maintenance features to minimize downtime.
- Drive System: Consider the type of drive system (mechanical or vibratory) that aligns with operational preferences and requirements.
- Environmental Considerations: Factor in environmental conditions such as temperature and humidity to ensure the screen’s longevity
Why Choose HPPA Rotary Screens?
- Durability and Build Quality:
- Problem: Rotary screens often face wear and tear due to the abrasive nature of materials processed.
- Solution: HPPA Crushers are known for their robust build quality and durable components, ensuring longevity and minimizing the risk of breakdowns.
- Maintenance Requirements:
- Problem: Regular maintenance can be time-consuming and costly, impacting production efficiency.
- Solution: HPPA Crushers are designed with user-friendly maintenance features, reducing downtime and the need for frequent interventions. This can contribute to increased operational efficiency.
- Screening Efficiency:
- Problem: Inadequate screening efficiency can lead to suboptimal product quality and increased energy consumption.
- Solution: HPPA Crushers are equipped with advanced screening technologies that enhance efficiency, ensuring precise separation and optimal throughput. This can result in higher quality end-products and energy savings.
- Adaptability to Different Materials:
- Problem: Some rotary screens struggle to handle a wide range of materials, limiting their versatility.
- Solution: HPPA Crushers are designed to handle diverse materials effectively. Their adaptability makes them suitable for various industries and applications, offering a versatile solution for different processing needs.
- Energy Efficiency:
- Problem: High energy consumption can contribute to operational costs and environmental impact.
- Solution: HPPA Crushers are designed with energy-efficient features, optimizing power consumption without compromising performance. This not only reduces operational costs but also aligns with sustainability goals.