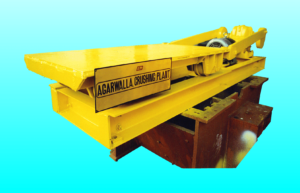
Reciprocating Feeder
Reliable Feeding, Unmatched Quality
What is a Reciprocating Feeder?
A Reciprocating Feeder is a robust and reliable feeding solution used in stone crushing equipment. Its primary function is to uniformly and continuously feed large chunks of raw material into crushers and screens, ensuring a steady and efficient flow throughout the crushing process.
Specifications include:
- 2-stage and 3-stage
- Capacity : 20 TPH to 500 TPH
- Feed size : 300 – 700 mm and below
- Output size : 40 mm and below
- Price : INR 1.0 – 5.5 crore
- Power Source : Electricity or diesel generators
- Flexibility : Customized based on specific requirements
How does a Reciprocating Feeder work?
The working principle of a Reciprocating Feeder involves a tray-like mechanism that moves back and forth in a linear motion. This reciprocating motion is powered by an electric motor, creating a pulsating flow of material onto the crusher or conveyor belt. The feeder’s adjustable stroke and speed allow operators to control the feed rate, optimizing the efficiency of the crushing operation.
Advantages of Reciprocating Feeders
- Consistent Feed Rate: The reciprocating motion ensures a uniform and steady material flow, preventing bottlenecks and optimizing the crusher’s performance.
- Versatility: Suitable for a wide range of materials, reciprocating feeders accommodate various sizes and types of granular materials.
- Customizable Stroke Length: Operators can adjust the stroke length to match the specific characteristics of the material, enhancing control over the feeding process.
- Durability: Built with rugged materials and precision engineering, reciprocating feeders are designed to withstand the harsh conditions of the stone crushing environment.
VSI Crushers Assembly Process
-
Fabrication of Components: Each component, from the feeder trough to the drive mechanism and support structure, undergoes precision fabrication. High-quality materials are selected to ensure durability and longevity.
-
Assembly of Frame and Support Structure: The frame, serving as the foundation of the feeder, is meticulously assembled. The support structure is integrated, providing the necessary stability to withstand the dynamic forces generated during operation.
-
Installation of Drive Mechanism: The electric motor, drive shaft, and associated components are expertly installed to create a robust and efficient drive mechanism. This stage is crucial for ensuring the precise reciprocating motion required for optimal feeding.
-
Calibration and Testing: Before leaving the manufacturing facility, each reciprocating feeder undergoes meticulous calibration and testing. The stroke length is adjusted, and the entire assembly is rigorously tested to guarantee consistent and reliable performance in the field.
-
Quality Assurance: Stringent quality control measures are implemented throughout the assembly process. From welding joints to electrical connections, every detail is scrutinized to meet industry standards and exceed customer expectations.
Types of Reciprocating Feeder
- Vibrating Grizzly Feeders:
-
- Ideal for pre-screening and removing fines before primary crushing.
- Robust construction to handle heavy-duty applications.
- Heavy-Duty Reciprocating Feeders:
-
- Designed for large, abrasive materials and high-capacity crushing plants.
- Built with reinforced components for extended durability.
- Medium-Duty Reciprocating Feeders:
-
- Versatile feeders suitable for a range of materials and moderate crushing applications.
- Balanced design for reliability and cost-effectiveness.
Checklist for Choosing the Best Reciprocating Feeder
- Material Characteristics: Consider the size, density, and abrasiveness of the material to ensure the feeder can handle specific requirements.
- Capacity Requirements: Determine the required feed rate and ensure the feeder’s capacity aligns with the crushing plant’s needs.
- Adjustability: Opt for a feeder with adjustable stroke and speed settings for fine-tuning the material flow.
- Build Quality: Choose a feeder with a robust and durable construction, capable of withstanding heavy-duty applications.
- Maintenance and Accessibility: Prioritize feeders with easy access points for maintenance to minimize downtime and operational disruptions.
- Safety Features: Check for safety features such as overload protection and emergency shutdown mechanisms to ensure worker safety.
- Compatibility: Ensure the feeder is compatible with the rest of the crushing equipment in your plant for seamless integration.
- Cost-Efficiency: Consider the initial cost, operational costs, and long-term maintenance expenses to determine the overall cost-effectivenes.
Why Choose HPPA Reciprocating Feeder?
- Durability and Build Quality:
- Problem: Reciprocating Feeders are subjected to heavy-duty usage in mining and other industries, leading to wear and tear.
- Solution: Opt for a brand that emphasizes durable construction and robust build quality. HPPA Crushers designed for Reciprocating Feeders often incorporate high-strength materials and advanced engineering, enhancing overall durability.
- Material Handling Efficiency:
- Problem: Inefficient material handling can result in jams, downtime, and reduced productivity.
- Solution: Choose a brand that offers Reciprocating Feeders with optimized material handling capabilities. HPPA Crushers are often tailored to work seamlessly with Reciprocating Feeders, ensuring efficient and reliable material flow.
- Customization Options:
- Problem: Standardized solutions may not meet specific operational requirements.
- Solution: Look for a brand that provides customization options to tailor the Reciprocating Feeder to your specific needs. HPPA Crushers, when integrated with Reciprocating Feeders, can be fine-tuned for the characteristics of the material being processed.
- Maintenance and Serviceability:
- Problem: Frequent breakdowns and challenging maintenance can lead to increased downtime.
- Solution: Prioritize brands that offer easy maintenance and quick serviceability features. HPPA Crushers often come with user-friendly maintenance designs, facilitating routine inspections and repairs to minimize downtime.
- Integration with Control Systems:
- Problem: Incompatibility with existing control systems can lead to operational inefficiencies.
- Solution: Ensure the chosen brand provides Reciprocating Feeders that seamlessly integrate with your control systems. HPPA Crushers are often designed with compatibility in mind, allowing for smooth integration and efficient control of the entire material handling process.