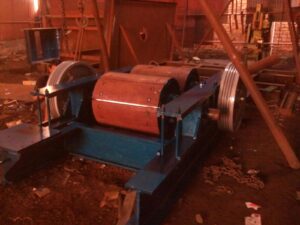
Roll Crusher
Capacity as promised
What is a Roll Crusher?
A jaw crusher is a machine used in the fields of mining, metallurgy, building materials, and highway engineering to reduce the size of large rocks, ores, and other materials. It operates by compressing the material between a stationary piece of steel (the jaw) and a moving piece (the swing jaw or movable jaw). The material is fed into the top of the crusher and is crushed as it moves down through the crushing chamber.
Specifications include:
- 2-stage and 3-stage
- Capacity : 20 TPH to 500 TPH
- Feed size : 300 – 700 mm and below
- Output size : 40 mm and below
- Price : INR 1.0 – 5.5 crore
- Power Source : Electricity or diesel generators
- Flexibility : Customized based on specific requirements
Roll Crushers Assembly Process
- Frame Assembly: The frame is the structural component that provides support for the other parts of the roll crusher. It is usually made of steel and is designed to withstand the heavy loads and stresses associated with the crushing process. The frame is assembled by welding or bolting together the various sections, creating a robust structure.
- Rolls Assembly: The rolls are the key crushing components of the roll crusher. They are typically made of high-strength steel. Each roll is mounted on a shaft, and the assembly may include bearings for smooth rotation.
- Drive Assembly: The drive assembly consists of motors, gears, and belts or chains that transmit power to the rolls. Motors provide the necessary torque to rotate the rolls at the desired speed. Gears and belts/chains transfer power from the motor to the rolls while allowing for adjustments in speed and torque.
- Feeding Mechanism: A feeding mechanism is incorporated to introduce the material to be crushed between the rolls. This can include a hopper or conveyor system that delivers the material to the crushing area.
- Adjustment Mechanism: Roll crushers often have an adjustment mechanism to control the gap between the rolls, regulating the size of the crushed material. This adjustment ensures flexibility in the final product size.
- Safety Features: Safety components such as guards and emergency stop systems are installed to protect operators from potential hazards during the operation of the roll crusher.
- Testing and Quality Control: Once the roll crusher is assembled, it undergoes testing to ensure all components are working correctly. Quality control measures may include checks on dimensions, alignment, and proper functioning of safety features.
Types of Roll Crushers:
- Single Roll Crushers: Have a single roll with a fixed shaft and a movable jaw.
- Double Roll Crushers: Have two rolls with either a single or double motor drive, allowing them to crush particles between the rolls.
- Triple Roll Crushers: Similar to double roll crushers, but with an additional third roll for finer crushing.
- Quad Roll Crushers: These crushers have four rolls, two fixed and two movable.
Checklist for Choosing the Best Roll Crusher:
- Type of Material: Different roll crushers are suitable for different materials. Some are better for hard and abrasive materials, while others are more effective for softer materials.
- Particle Size: Determine the desired final particle size of the crushed material, as different roll crushers are designed for different size ranges.
- Capacity Requirements: Consider the required capacity of the crusher, as different types and sizes of roll crushers have varying throughput capacities.
- Maintenance Requirements: Assess the ease of maintenance and the availability of spare parts. This is crucial for ensuring the longevity and efficiency of the equipment.
- Energy Efficiency: Evaluate the energy efficiency of the roll crusher, as this can impact operational costs.
- Feed Size and Product Size Control: Check the ability of the roll crusher to handle the size of the incoming feed and produce the desired product size. Some crushers come with features for adjusting the gap between the rolls to control the final product size.
- Space and Installation Constraints: Consider the available space and installation requirements, especially if the crusher needs to be integrated into an existing processing plant.
- Cost and Budget Constraints: Evaluate the initial cost, operating costs, and overall budget constraints to choose a roll crusher that provides the best value for the investment.
Why Choose HPPA Roll Crushers?
- Durability and Build Quality:
- Problem: Roll crushers may face issues related to wear and tear, leading to frequent maintenance and downtime.
- Solution: Opt for a brand known for durable construction and high-quality materials. HPPA Crushers are recognized for their robust build, ensuring longevity and reducing the need for constant repairs.
- Performance and Efficiency:
- Problem: Inconsistent or low performance can result in inefficient crushing processes and reduced productivity.
- Solution: Choose a brand that emphasizes high-performance features and efficient crushing capabilities. HPPA Crushers are designed for optimal efficiency, providing consistent and reliable performance.
- Ease of Maintenance:
- Problem: Roll crushers may require complex or time-consuming maintenance procedures, impacting overall operational efficiency.
- Solution: Prioritize brands that offer user-friendly designs and easy maintenance features. HPPA Crushers often incorporate simplified maintenance processes, minimizing downtime and enhancing ease of use.
- Adaptability to Various Materials:
- Problem: Some roll crushers may struggle with processing different types of materials, limiting their versatility.
- Solution: Look for a brand that offers versatility in handling a wide range of materials. HPPA Crushers are designed to handle various materials effectively, ensuring adaptability to different crushing applications.
- Safety Features:
- Problem: Safety concerns during the operation of roll crushers can lead to accidents and injuries.
- Solution: Prioritize brands that integrate advanced safety features into their designs. HPPA Crushers often come equipped with safety mechanisms to protect operators and prevent accidents during operation.