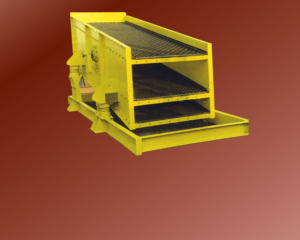
Vibrating Screen
Efficient. Cost-Effective. Powerful
What is a Vibrating Screen?
A vibrating screen is a versatile and indispensable equipment used in various industries for sorting and separating materials based on their particle size. It is a high-efficiency sieving device that utilizes vibrational motion to facilitate the separation process.
Place and Order
Key Features:
- Vibration Mechanism: The heart of a vibrating screen lies in its vibratory mechanism. Typically, it comprises an eccentric shaft that rotates to generate the required vibrations. These vibrations convey energy to the screen mesh, causing particles to move and separate based on size.
- Screen Mesh: The screen mesh is a critical component, consisting of tightly woven wires or perforated plates. It acts as a filter, allowing smaller particles to pass through while retaining larger ones. The choice of mesh size is crucial and depends on the application and desired particle separation.
- Deck Configuration: Vibrating screens can have multiple decks stacked on top of each other. Each deck contributes to the sorting process, making the equipment highly efficient in handling different particle sizes simultaneously.
- Applications: From mining and construction to recycling and agriculture, vibrating screens find application in diverse industries. They are used to classify, separate, and dewater various materials, ranging from aggregates and minerals to chemicals and pharmaceuticals.
Advantages:
- Efficient Sorting: Vibrating screens excel in efficiently sorting materials based on size, leading to improved production processes.
- Versatility: With adjustable settings and deck configurations, vibrating screens can handle a wide range of materials and applications.
- Reduced Downtime: Robust construction and minimal maintenance requirements contribute to increased operational uptime
Specifications include:
- 2-stage and 3-stage
- Capacity : 20 TPH to 500 TPH
- Feed size : 300 – 700 mm and below
- Output size : 40 mm and below
- Price : INR 1.0 – 5.5 crore
- Power Source : Electricity or diesel generators
- Flexibility : Customized based on specific requirements
Place and Order
Vibrating Screen Assembly Process
-
Frame Construction: The foundation of a vibrating screen is its sturdy frame. Components are precisely welded or bolted together to create a robust structure. The frame supports the entire assembly and provides a stable base for the vibrating mechanism.
-
Vibratory Mechanism Integration: The eccentric shaft, bearings, and other vital components of the vibratory mechanism are carefully integrated into the frame. This is a critical step as the seamless functioning of the vibrating screen relies on the precise alignment and assembly of these parts.
-
Screen Mesh Installation: Attaching the appropriate screen mesh is crucial for achieving the desired particle separation. Whether it’s wire mesh or perforated plates, skilled technicians ensure a secure and accurate installation, taking into account factors like tension and mesh size.
-
Motor and Drive System: The motor and drive system, responsible for generating the vibrations, are installed with precision. Proper alignment and calibration are essential to achieve the desired amplitude and frequency, optimizing the screening process.
-
Quality Checks: Before the vibrating screen leaves the assembly line, thorough quality checks are conducted. This includes inspecting welds, verifying alignment, and testing the functionality of the vibratory mechanism to ensure that the equipment meets the highest standards.
-
Final Calibration: Once assembled, the vibrating screen undergoes final calibration to fine-tune settings for specific applications. This step ensures that the equipment is ready to deliver optimal performance in its intended environment.
Types of Vibrating Screens:
- Linear Vibrating Screen: Ideal for medium to coarse-grained materials. Linear motion facilitates efficient screening of bulk materials.
- Circular Vibrating Screen: Versatile design suitable for various material types. Circular motion improves screening efficiency.
- Elliptical Vibrating Screen: Offers a combination of linear and circular motion. Efficient for screening sticky and difficult-to-screen materials.
- High-Frequency Vibrating Screen: Designed for fine particle separation. Utilizes high-frequency vibration for improved screening accuracy.
- Inclined Vibrating Screen: Inclined at an angle to enhance material flow. Ideal for screening heavy and abrasive materials.
Checklist for Choosing the Best Vibrating Screen:
- Material Characteristics: Understand the properties of the materials to be screened (e.g., size, moisture content, abrasiveness).
- Capacity Requirements: Determine the desired screening capacity to match the production needs.
- Mesh Type and Size: Select the appropriate mesh type and size to achieve the desired particle separation.
- Screening Efficiency: Evaluate the screen’s efficiency in terms of the percentage of material passing through the mesh.
- Maintenance and Accessibility: Opt for screens with easy access for maintenance and screen replacement.
- Vibration Mechanism: Consider the type of vibration mechanism (e.g., unbalanced exciter, electromagnetic) based on application requirements.
- Installation and Footprint: Ensure the vibrating screen can be easily installed within the existing processing plant layout.
Why Choose HPPA Vibrating Screen?
- Durability and Longevity:
- Problem: Vibrating screens may face wear and tear due to the continuous and abrasive nature of material processing, leading to frequent replacements and downtime.
- Solution: HPPA crushers are designed for enhanced durability and longevity, reducing the need for frequent replacements and minimizing downtime.
- Efficient Material Screening:
- Problem: Inefficient material screening can result in undersized or oversized particles, impacting the quality of the final product.
- Solution: HPPA crushers offer precise particle size control, ensuring efficient material screening and consistent product quality in vibrating screen applications.
- Maintenance and Ease of Service:
- Problem: High maintenance requirements can lead to increased operational costs and downtime.
- Solution: HPPA crushers are engineered for ease of maintenance, with features that simplify servicing and reduce downtime, contributing to overall operational efficiency.
- Energy Efficiency:
- Problem: Traditional vibrating screens may consume excessive energy, contributing to higher operational costs and environmental impact.
- Solution: HPPA crushers are designed with energy efficiency in mind, offering advanced technologies to minimize energy consumption during the material crushing process.
- Adaptability to Different Materials:
-
- Problem: Vibrating screens may struggle to handle diverse materials with varying characteristics, leading to suboptimal performance.
- Solution: HPPA crushers are versatile and can adapt to a wide range of materials, ensuring consistent and efficient processing across various applications, enhancing the overall flexibility of the material handling system.
Place and Order